In today’s dynamic marketplace, efficiency and agility are crucial for business success. An increasingly popular approach to achieving this is the implementation of the Kanban inventory system. This methodology streamulates operations and enables companies to respond to demand without overburdening resources. The benefits are extensive, ranging from cost savings to enhanced productivity. Below, we explore how Kanban can revolutionize inventory management and propel businesses forward.
Embracing Efficiency with Kanban Inventory Management
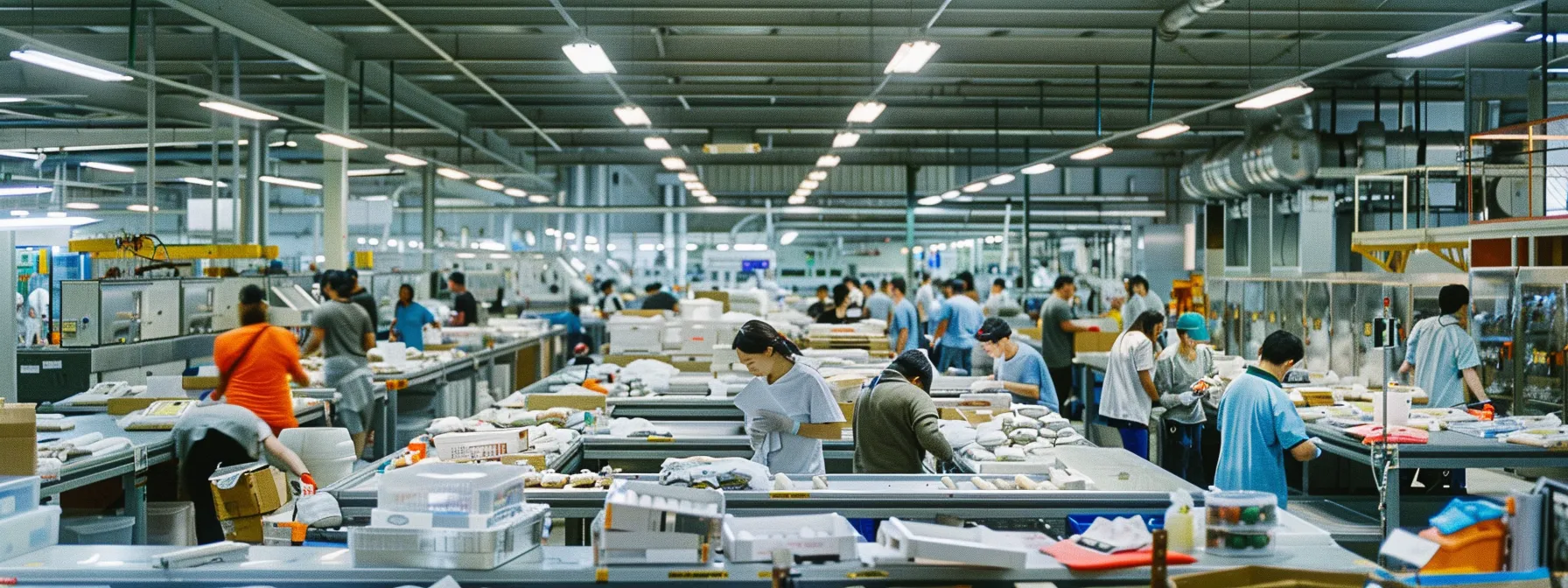
Efficiency is key in business operations, and a Kanban inventory system helps companies streamline their processes by responding directly to demand rather than forecasts. This system uses visual cues to indicate when it’s time to reorder or produce more items, minimizing idle time and reducing inventory holding costs. By pulling tasks through the system only when needed, businesses can align work with customer needs, cut down on overproduction, and maintain a synchronized workflow.
Kanban also makes it easy to identify and address bottlenecks in the production process. With its visible workflow, managers can quickly spot underperforming areas and take corrective actions to ensure consistent productivity. The flexibility of the Kanban inventory system allows companies to adapt swiftly to changes in demand or market conditions, providing a competitive edge by enabling quick pivots without major disruptions.
Reducing Waste and Increasing Productivity Through Kanban
The Kanban inventory system is a lean manufacturing approach that focuses on reducing waste without sacrificing productivity. It eliminates overproduction, a costly form of waste, by producing only what is needed when needed. This reduces storage costs and the risk of obsolescence. Kanban also helps in reducing wasted time and effort by reducing planning and reworking schedules.
Visual kanban cards communicate production and inventory status, reducing misunderstandings and the need for corrective actions. Kanban encourages ongoing productivity improvements by identifying and implementing incremental changes that improve speed and quality over time. This iterative approach fosters a culture of productivity that benefits the entire organization. The simplicity of the Kanban system empowers all employees to contribute to the efficiency of operations.
Achieving Just-in-Time Delivery with Kanban Principles
The Kanban system is a highly disciplined and time-sensitive control mechanism that aligns with the principles of Just-in-Time (JIT) delivery. It helps companies reduce costs associated with large inventory holdings by ensuring components arrive exactly as needed. Kanban fosters a proactive culture where teams anticipate production line needs and trigger replenishment when low inventory levels are detected.
This minimizes wait times and keeps the production line moving, increasing customer satisfaction. Kanban also helps in producing high-quality products by reducing the risk of damage or deterioration and allowing for swift corrective actions. With JIT principles, inventory costs are kept at a minimum without the risk of stockouts. Kanban’s real-time tracking and visual cues provide a strategic advantage in inventory management.
Enhancing Visibility and Collaboration in Supply Chain Management
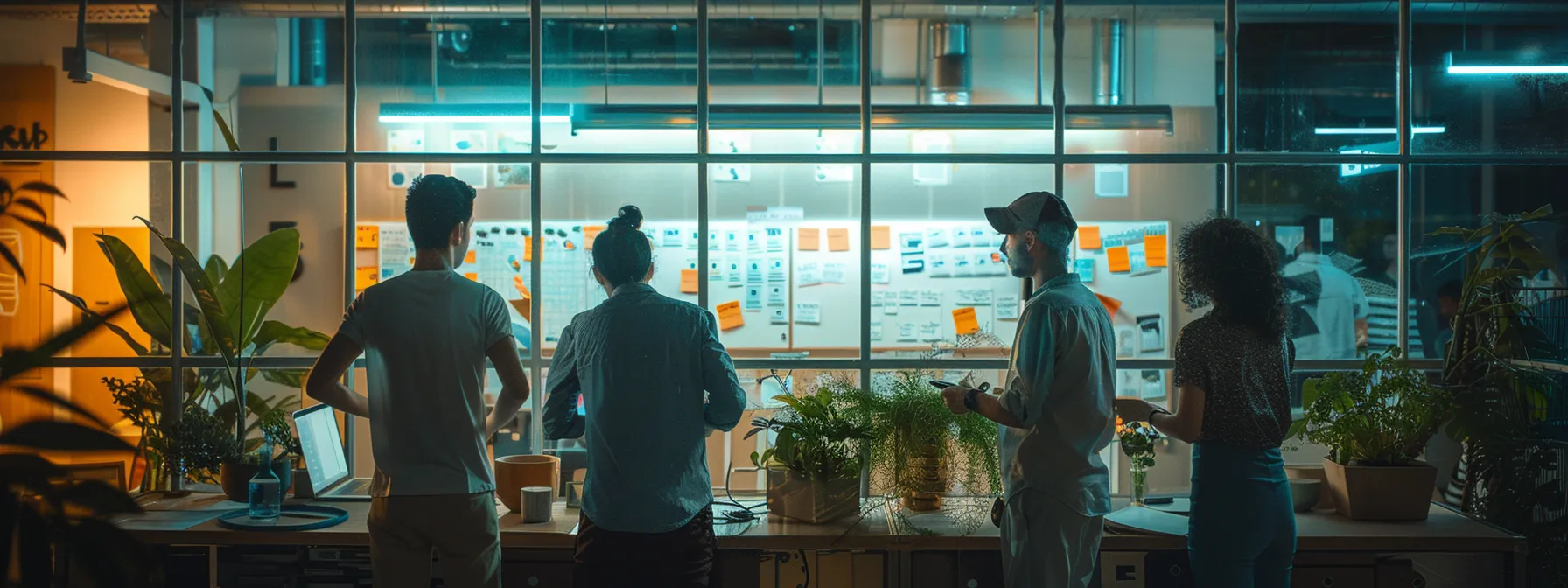
Kanban systems are crucial for effective supply chain management due to their transparency, which allows for better control, communication, and collaboration across departments. Kanban boards, both physical and digital, serve as focal points for team discussions and planning, leading to innovative solutions for complex supply chain challenges.
This increased visibility fosters a sense of collective responsibility, enabling teams to optimize workflow and realign quickly if production requirements or customer demand change. Kanban fosters an environment where information is shared openly, enhancing the supply chain’s ability to respond cohesively, leading to better outcomes, higher efficiency, and a more resilient supply chain. This is essential for ensuring synchronization across the supply chain and overcoming challenges.
Measuring Success: Key Performance Indicators for Kanban Implementation
Kanban systems are effective in reducing waste and improving efficiency. Key Performance Indicators (KPIs) that businesses should monitor include cycle time, lead time, inventory levels, and customer satisfaction metrics. Cycle time indicates a decrease in production, while lead time shows an improvement in responsiveness and customer service. Inventory levels are another crucial KPI, with a reduction in excess inventory reflecting the system’s ability to meet demand.
Consistently low work-in-progress (WIP) inventory indicates good system functioning. Customer satisfaction metrics, such as on-time delivery rates, product quality, and customer feedback, provide a comprehensive picture of how well inventory management practices support end goals. Continuous improvement is the hallmark of kananban, and tracking these KPIs ensures the system remains dynamic and productive.
Overall, the adoption of a Kanban system can be a transformational move for a business seeking leaner, more responsive, and collaborative operations. By leveraging the principles of kanban, companies can create an environment where efficiency and continual improvement are not just goals, but a reality that drives their success every day.